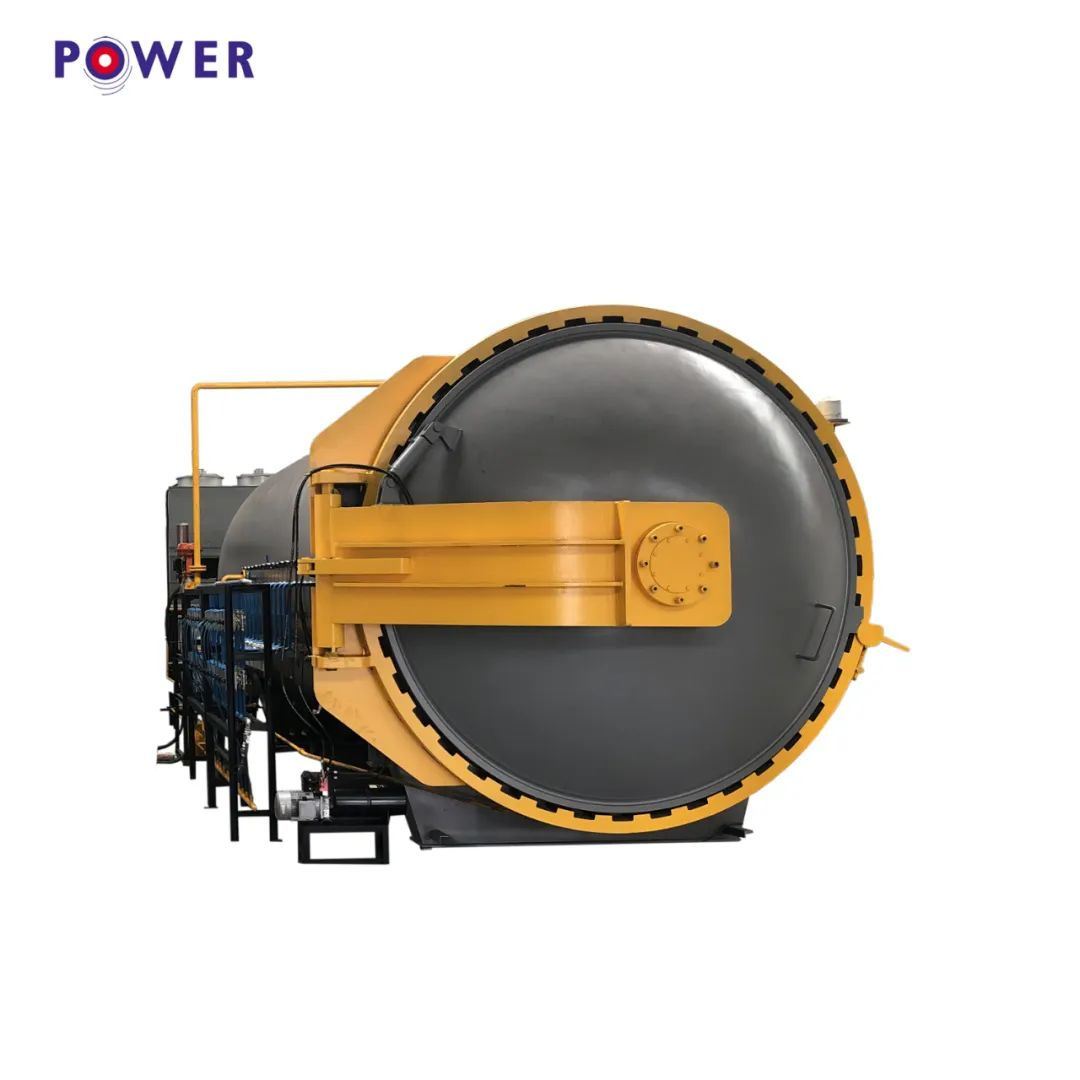
تأثير الفلكنة على بنية وخصائص المطاط:
تعتبر الفلكنة خطوة مهمة في عملية تصنيع المنتجات المطاطية ، وهي عملية التحول من الهيكل الخطي إلى بنية الجسم ، مما يؤدي إلى تغييرات شاملة بما في ذلك الخصائص المادية والميكانيكية ، ومقاومة درجة الحرارة ، ومقاومة المذيبات ، ومقاومة التآكل ، وتعزيز القيمة وتطبيق المنتج.
يخضع هيكل وخصائص المطاط لتغييرات كبيرة قبل وبعد الفلكنة. تحتوي جزيئات المطاط قبل الفلكنة على هيكل خطي مع قوى Van der Waals التي تعمل بينهما ، وتظهر اللدونة الجيدة والاستطالة ، وكذلك الذوبان. أثناء عملية الفلكنة ، يتم تشغيل الجزيئات وتخضع للتفاعلات بين الارتباط بين الكيميائية ، مما يشكل بنية شبكة حيث يتم ربط الجزيئات بواسطة الروابط الكيميائية.
تشمل هيكل وخصائص المطاط الفلكان بشكل أساسي:
الهيكل: الروابط الكيميائية ، موقف الروابط المتقاطعة ، درجة الارتباط المتقاطع ، والربط المتقاطع
الأداء: الخصائص الميكانيكية (قوة الاستطالة المستمرة ، صلابة ، قوة الشد ، الاستطالة ، المرونة) ، الخواص الفيزيائية ، الاستقرار الكيميائي بعد الفلكنة
يمكن لعملية الفلكنة تغيير خصائص المطاط بشكل كبير. أخذ المطاط الطبيعي كمثال ، مع زيادة درجة الفلكنة:
التغيرات في الخواص الميكانيكية: زيادة المرونة ، قوة الشد ، قوة الشد ، قوة المسيل للدموع ، صلابة ، انخفاض الاستطالة ، التشوه الدائم للضغط ، وتوليد حرارة التعب
التغيرات في الخواص الفيزيائية: لا يمكن حل نفاذية الهواء ونفاذية الماء ، ولا يمكن حلها ، ولا يمكن أن تتضخم إلا ، وتحسن مقاومة الحرارة ، وتحسن الاستقرار الكيميائي ، يزيل التفاعل المتبادل مجموعات أو ذرات نشطة للغاية ، مما يجعل تفاعل الشيخوخة صعبًا. يعيق بنية الشبكة انتشار الجزيئات المنخفضة ، مما يجعل من الصعب على الجذور الحرة من المطاط الانتشار.
إن ظروف الفلكنة ، بما في ذلك الضغط ودرجة الحرارة والوقت ، هي العوامل الرئيسية التي تحدد نتائج الفلكنة. يكون لضغط الفلكنة تأثير مهم على منع تكوين الفقاعات في المادة المطاطية ، مما يؤدي إلى تحسين ضغط المواد المطاطية ، وملء القالب بالمواد المطاطية. يمكن أن يحسن الالتصاق بين الطبقات المختلفة (طبقة المطاط وطبقة القماش أو طبقة المعادن ، طبقة القماش وطبقة القماش) في المنتج ، وتحسين الخواص الفيزيائية للمطاط الفلكان (مثل مقاومة الانحناء).
درجة حرارة الفلكنة هي الحالة الأساسية لتفاعل الفلكنة ، والتي يمكن أن تؤثر بشكل مباشر على سرعة الفلكنة ، وجودة المنتج ، والفوائد الاقتصادية للمؤسسة. يمكن أن يؤدي رفع درجة حرارة الفلكنة إلى تسريع سرعة الفلكنة وتحسين كفاءة الإنتاج ، ولكن يمكن أن تؤدي درجة حرارة الفلكنة المفرطة إلى مشاكل مثل كسر السلسلة الجزيئية المطاطية ، وعكس الفلكان ، وانخفاض الخصائص الميكانيكية للمواد المطاطية ، وانخفاض قوة المنسوجات. يمكن أن تقصر أيضًا وقت الحارقة للمواد المطاطية ، مما تسبب في نقص المطاط المحلي وتفكيك المنتجات غير المتكافئة. لذلك ، يجب أن ينظر اختيار درجة حرارة الفلكنة بشكل شامل في عوامل مثل نوع المطاط ونظام الفلكنة وهيكل المنتج.
يعد تحديد ظروف الفلكنة - بما في ذلك الضغط ودرجة الحرارة والوقت - عملية معقدة تتطلب النظر في عوامل متعددة.
ضغط الفلكنة: يعتمد اختيار ضغط الفلكنة بشكل أساسي على تصميم ومتطلبات المنتجات المطاطية. بشكل عام ، يتم تحديد اختيار الضغط بشكل أساسي حسب شكل المنتجات المطاطية وحجمها وتعقيدها. كلما زاد الضغط ، كان سيولة المطاط أفضل ، والتي يمكن أن تملأ القالب بشكل أفضل. في الوقت نفسه ، يمكن للضغط العالي أن يمنع بفعالية توليد الفقاعات ويحسن من انضغاط المنتج. ومع ذلك ، قد يؤدي الضغط المفرط إلى تدفق مفرط للمادة المطاطية ، مما يسبب التشويه في شكل المنتج.
درجة حرارة الكبريت: تؤثر درجة حرارة الفلكنة بشكل مباشر على سرعة وجودة تفاعل الفلكنة. كلما ارتفعت درجة الحرارة ، زادت تفاعل الفلكنة بشكل أسرع ، ولكنه قد يتسبب في كسر السلاسل الجزيئية المطاطية ، مما يؤثر على الخواص الفيزيائية للمنتج. يمكن أن تضمن درجة حرارة الفلكنة المناسبة سرعة فلكانية جيدة دون التسبب في تلف حراري كبير للمواد المطاطية.
وقت الكبريت: يرتبط وقت الفلكنة ارتباطًا مباشرًا بدرجة حرارة الفلكنة. قد تتطلب درجات الحرارة المرتفعة أوقاتًا فلكية أقصر ، والعكس صحيح. بشكل عام ، يحتاج اختيار وقت الفلكنة إلى النظر في نوع المواد المطاطية ، ودرجة حرارة الفلكنة ، وسمك المنتج. يمكن أن يضمن وقت الفلك الأمثل المحدد من خلال التجارب أن مواد المطاط تحقق الخواص الميكانيكية المثلى ومقاومة الشيخوخة.
بشكل عام ، يعد تحديد ظروف الفلكنة عملية تتطلب دراسة شاملة لعوامل مختلفة مثل نوع المواد المطاطية وشكل المنتج ومعدات الفلكنة ، وما إلى ذلك في الإنتاج الفعلي ، وعادة ما يكون من الضروري إجراء تجارب متعددة وتحسين ظروف الفلكنة تدريجياً للحصول على أفضل أداء للمنتج.
وقت النشر: يناير -09-2024